Corrosion Under Insulation (CUI) Resource Library
Thermal insulation is an integral part of the industrial complex, and it offers a variety of benefits. Designing, installing and maintaining an insulation system to address corrosion under insulation (CUI) is a critical step to preemptively preventing CUI. At Johns Manville, we recognize that this task includes incorporating many details from material specifications to the latest research and technology. We have researched this crucial topic extensively and have created a library of resources to help you design, install and maintain better insulation systems. Here you’ll find Insulation Intel® webinars, blogs, technical bulletins, infographic and eBooks to support your CUI mitigation strategy.
- What is Corrosion Under Insulation
- Protecting Equipment and Assets from Corrosion Under Insulation
- What is the XOX Corrosion Inhibitor®
- Industry Leading Testing for Corrosion Under Insulation
- Insulation Coatings vs. Traditional Insulation
- Insulation Products that Inhibit Corrosion Under Insulation
- Additional CUI Resources
Corrosion Under Insulation (CUI) refers to the corrosion of piping, pressure vessels and structural components resulting from water trapped under insulation. In the simplest terms, CUI is any type of corrosion that occurs due to moisture present on the external surface of insulated equipment. The damage/attack can be caused by one of multiple factors, and can occur in equipment operating at ambient, low, and heated services, depending upon conditions.

Protecting Equipment and Assets From Corrosion Under Insulation
Insulation systems, comprised of thermal insulation, jacketing, mastics, and sealants, are designed to keep water out in order to maintain the integrity of the thermal insulation and limit corrosion under insulation (CUI). However, even the best designed and installed systems sometimes become compromised in real-world applications, resulting in the presence of water at the pipe surface and the potential for CUI. As such, it is essential to understand how the chemistry of thermal insulation affects CUI potential including the role of hydrophobic insulation, corrosion inhibitors, drying out wet insulation and utilizing Risk-Based Inspection (RBI) programs.
Hydrophobic Insulation
While specifying hydrophobic insulation materials can help prevent water from penetrating into the system, most insulations with a hydrophobic treatments are silicone-based additives that are organic in nature. As such, these types of silicone-based hydrophobic treatments begin to burn off around 450°F and become ineffective. We discuss this in detail in our webinar all about How Hydrophobic Insulation Impacts CUI.
The XOX Corrosion Inhibitor®
The XOX Corrosion Inhibitor is a proprietary corrosion inhibitor that is integral to the chemical makeup of Thermo-1200® Calcium Silicate and Sproule WR-1200® Expanded Perlite industrial insulations. The XOX Corrosion Inhibitor helps protect against corrosion under insulation and makes Thermo-1200 one of the least corrosive high-temperature insulations available. We explain more in our blog, Understanding the Mechanisim and Longevity of Corrosion Inhibitors.
Drying Out Wet Insulation
More recently, specifying water repellent insulations has become a popular practice. However, this approach is often too simplistic to account for all the potential water ingress scenarios. Rather than relying on water repellent insulation as the panacea, a better approach is to design an insulation system around the assumption that water will eventually enter the system. Designers could allow for means of water egress, such as weep holes. In this white paper, we explore various insulation system configurations to dry out wet insulation.
The XOX Corrosion Inhibitor is a proprietary corrosion inhibitor that is integral to the chemical makeup of Thermo-1200® Calcium Silicate and Sproule WR-1200® Expanded Perlite industrial insulations. Insulation materials with the XOX Corrosion Inhibitor were shown to decrease the proliferation of corrosion on metal surfaces by depositing a protective coating layer onto the metal surface. This layer was present when testing the Thermo-1200 with XOX Corrosion Inhibitor and the Sproule WR-1200 with XOX Corrosion Inhibitor sample. The surface layer that developed from the corrosion inhibiting properties had a chemical composition that was consistent with documented standard ASTM C795 requirements for limiting stress corrosion cracking of stainless steel.
Concerns with corrosion inhibitors in insulation are typically related to the longevity of the inhibitor activity; however, it was shown in a study that the protective attributes of the XOX Corrosion Inhibitor does not appear to decrease over time when cycled between wet and dry states with either tap or salt water. Exploring the resources below and utilizing these findings can be the first step in building a comprehensive corrosion mitigation strategy and prolonging the life of assets and insulation systems.
A visual overview of the mechanism and longevity of the XOX Corrosion Inhibitor®
Understand how the insulation chemistry can influence the potential for corrosion of the system as a whole.
Industry experts explore new ways to mitigate CUI and a new strategy based on the chemistry of the insulation.
Industry Leading Testing for Corrosion Under Insulation
While specifiers, contractors and facility owners tend to bear the burden of preventing corrosion under insulation (CUI) by designing systems that can inhibit CUI, installing them according to the specification to ensure that they work effectively, and consistent accountability for maintenance, manufacturers can also play a role in contributing to successful corrosion prevention. While it may seem like the role would be limited to offering materials with features like corrosion inhibitors or hydrophobicity, Johns Manville is of the opinion that there is more to it. We take it a step further to understand the intricacies of the interactive relationship between insulation and the corrosion that can occur beneath it is critical to creating and manufacturing materials that contribute to a defensive CUI protection strategy.
Insulation Intel®: A Systems Application Approach to Corrosion Testing Part 1
As part of our on-going focus to understand our products in various applications, we initiated a testing program at a third-party testing agency to evaluate products and test protocols under accelerated and/or severe CUI (corrosion under insulation) conditions within a system.
Insulation Intel®: A Systems Application Approach to Corrosion Testing Part 2: The Corrosion Results
Thin blanket insulations were tested by exposing the assemblies to conditions that accelerate and promote corrosion and replicate real-world conditions. At the conclusion, the third-party agency analyzed the results, and we compared them to laboratory data based on ASTM specifications.
Insulation Intel®: A Systems Application Approach to Corrosion Testing Part 3: The Thermal Results
In Part 3, we reviewed the results of the long-term thermal testing and in our view, the test results reveal critical data to consider when designing insulation thicknesses and attempting to minimize labor and material costs.
The primary function of thermal insulations is to reduce the rate of heat transfer. Industrial insulation coatings are often promoted by manufacturers as a viable alternative to traditional insulations. While this viability may be true in some applications, the performance characteristics of coatings and traditional insulations are dramatically different. The distinguishing factor is that traditional insulations meet a broader range of safety requirements by reducing heat transfer and meeting safe-to-touch requirements. This Insulation Intel® technical bulletin compares the advantages and disadvantages of using thermal insulation coatings versus traditional insulation products based on third-party testing.
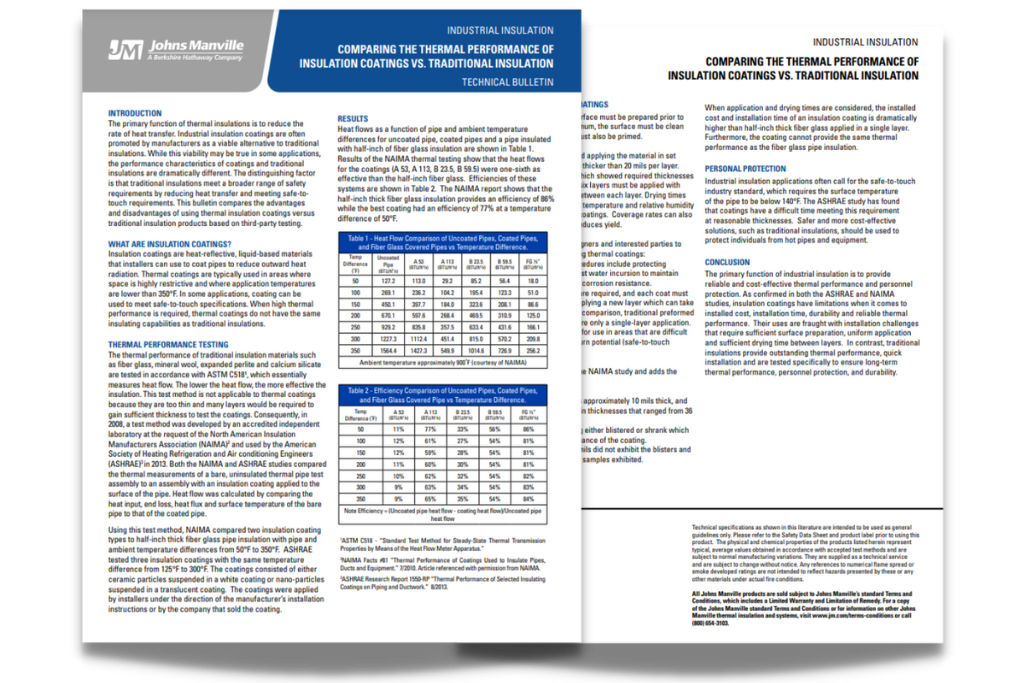
Perlite Insulation
Sproule WR-1200® is a pre-formed, high-temperature, non-wicking pipe and block insulation. It is produced with XOX Corrosion Inhibitor®, a distinctive formula that inhibits corrosion to outside surfaces of pipe and equipment, especially stress corrosion cracking of austenitic stainless steel.
NEW! Insulation Intel® eBook Series: XOX Corrosion Inhibitor®
Exploring the Mechanism and Longevity of Corrosion Inhibitors in Insulation
Insulation Intel® eBoook Series: CUI
The Comprehensive Results from "Real-World" Corrosion Under Insulation Test Protocols
Insulation Intel® eBook Series: Thin Blanket Insulations
Considerations for Thin Blanket Insulations for Industrial Applications